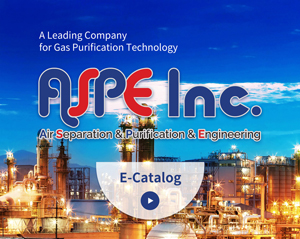
Hydrogen Plant,gas dryer Solutions for a Sustainable Future
As a specialized gas engineering company, we provide solutions across various industries based on air separation, gas dryer purification, and hydrogen plant technologies.
ASPE provide comprehensive services across various industries, specializing in air separation units, hydrogen plants and purification systems, gas purification systems, and gas dryer engineering solutions.
ASPE is a leading company providing hydrogen plant solutions for a sustainable future. Through innovative approaches in hydrogen production, storage, and distribution technologies, we are building eco-friendly energy systems. As a specialized gas engineering company with expertise in air separation and gas purification technologies, ASPE has established itself as a trusted partner in the global market. We offer the best hydrogen plant solutions to our customers, enhancing energy efficiency, reducing carbon emissions, and creating a sustainable energy environment for a better future. A hydrogen plant is a specialized industrial facility designed for large-scale hydrogen production, playing a crucial role in the hydrogen economy. Among the various hydrogen production methods, Steam Methane Reforming (SMR) is the most widely used, accounting for approximately 76% of global industrial hydrogen production. In a hydrogen plant utilizing SMR, natural gas (primarily methane) reacts with steam at high temperatures (700-1000°C) and pressures (3-25 bar) in the presence of a catalyst to produce hydrogen. This reaction generates carbon monoxide and hydrogen (CH₄ + H₂O → CO + 3H₂), followed by a Water-Gas Shift reaction, which yields additional hydrogen (CO + H₂O → CO₂ + H₂). Finally, Pressure Swing Adsorption (PSA) technology is used in the hydrogen plant to separate high-purity hydrogen. The overall energy efficiency of an SMR-based hydrogen plant is approximately 65-75%, making it the most cost-effective approach to hydrogen production. Another key hydrogen production technology employed in a hydrogen plant is Water Electrolysis, which utilizes electricity to split water into hydrogen and oxygen (2H₂O → 2H₂ + O₂). This method is gaining attention as it enables hydrogen plants to produce green hydrogen when powered by renewable energy sources. Hydrogen plants using electrolysis can implement different technologies, including Alkaline Electrolysis, Proton Exchange Membrane (PEM) Electrolysis, and Solid Oxide Electrolysis (SOEC). Alkaline electrolysis operates at 70-90°C with an efficiency of 60-70%, while PEM electrolysis works at 50-80°C with an efficiency of 65-75%. SOEC electrolysis, operating at 700-900°C, boasts an efficiency of 75-85%, making it a highly efficient next-generation technology. Hydrogen plants integrating water electrolysis technology are instrumental in reducing carbon emissions and expanding the adoption of sustainable energy solutions. In addition to SMR and electrolysis, some hydrogen plants utilize Gasification technology, which converts coal or biomass into hydrogen. This process involves heating carbon-containing materials at 800-1800°C in an oxygen-limited environment to produce syngas (CO, H₂), which is further refined through the Water-Gas Shift reaction. While the efficiency of a hydrogen plant using gasification is lower (around 45-55%), this method offers the advantage of using low-cost raw materials. A hydrogen plant consists of several key systems, including a feedstock pretreatment system, reactor system, gas purification system, control and safety system, and utility system. The feedstock pretreatment system removes impurities and desulfurizes raw materials before they enter the reactor system, which includes reformers, gasifiers, or electrolyzers, depending on the hydrogen production method used in the hydrogen plant. The gas purification system ensures the production of high-purity hydrogen using PSA, membrane separation, and cryogenic separation technologies. The control and safety system within a hydrogen plant manages operations through Distributed Control Systems (DCS) and gas leak detection technologies, ensuring safe and efficient production. The utility system provides essential support functions such as cooling water, nitrogen, and steam, which are vital for maintaining stable hydrogen production in the hydrogen plant. The scale of a hydrogen plant is classified based on production capacity into small-scale (100-1,000 Nm³/h), medium-scale (1,000-10,000 Nm³/h), large-scale (10,000-100,000 Nm³/h), and extra-large (above 100,000 Nm³/h). Future advancements in hydrogen plant technology will likely include Auto-Thermal Reforming (ATR) and Partial Oxidation (POX), which integrate Carbon Capture technologies to enhance sustainability. Additionally, high-efficiency electrolysis systems such as Anion Exchange Membrane (AEM) electrolysis are expected to further improve the performance of hydrogen plants. These innovations will enhance hydrogen production efficiency and reduce costs, accelerating the global adoption of hydrogen plants as essential components of a sustainable energy infrastructure. ASPE Inc. plays a crucial role in the hydrogen plant sector by offering hydrogen purification and recovery technologies, hydrogen generation systems, air separation and gas engineering solutions, and hydrogen storage and transportation systems. The company specializes in PSA and membrane-based purification systems, enabling hydrogen plants to recover high-purity hydrogen from industrial processes. ASPE also develops hydrogen production equipment compatible with electrolysis and reforming methods, catering to the diverse technological needs of modern hydrogen plants. Furthermore, ASPE provides air separation units for nitrogen and oxygen production along with comprehensive gas engineering services to optimize hydrogen plant operations. Additionally, the company supplies high-pressure hydrogen storage solutions, ensuring safe and efficient hydrogen transportation. By offering turnkey solutions for hydrogen plant design, engineering, manufacturing, and maintenance, ASPE has established itself as a trusted partner for hydrogen plant projects worldwide. With its expertise in hydrogen plant technologies, ASPE is actively contributing to the development of a sustainable hydrogen economy, playing a critical role in advancing the future of hydrogen production.